In recent years, energy saving and emission reduction has become the trend of the time and lightweight of automobile is also general trends. Under the background of the two trends, aluminum alloy materials are more widely used in automobiles; more and more automobile parts are made by die casting processes. As core components of automobiles, engine blocks mainly adopt
aluminum alloy and cast iron as the materials; among these two materials, aluminum alloy cylinder blocks gain more and more recognition; car corporations from Japan, South Korea, Europe and the United States mostly use
die casting aluminum alloy cylinder blocks.
In production fields of cylinder blocks, ordinary sand mould cast iron cylinder blocks have advantages of simple processes, low costs, good rigidity and heat resistance, but they also have a disadvantage; that is, sand mould cast iron cylinder blocks are overweight. If we divide the cylinder block into lower crankshafts and upper cylinder jackets two parts, we will adopt
aluminum alloy for the lower part and cast iron for the upper part; by doing this, we can not only reduce weights of cylinder blocks, but also keep advantages of cast iron cylinder blocks.
Lower cylinder blocks refer to the lower crankshafts of the engines after we divide cylinder blocks into two parts. Lower cylinder blocks are parts with thick wall and their wall thickness have great differences; therefore, lower cylinder blocks are very difficult to be made by die casting processes. Learning from the related experience at home and abroad, we design and develop die casting technology for lower cylinder blocks based on an engine with 1.5 tons and the experiment is very successful.
Difficulties of die casting aluminum alloy cylinder blocks
The weight of the aluminum alloy cylinder block die cast is 8.4 kilograms; the overall dimension is 382 mm X 258 mm X 67 mm; the weight of the die cast is 11.1 kilograms; the material is A380 and the average wall thickness is 7.2 mm. Lower cylinder blocks and crankshafts are connected; therefore, we should place cast iron inserts at bottoms of cylinder blocks.
Lower cylinder blocks die casting processes are complex and the main difficulties of the processes are as the following.
1. Five pieces of cast iron inserts should be placed on die casts and they should be perfectly inlaid into
aluminum alloy die casts.
2. The thinnest lower cylinder block's wall thickness is 2 mm; the thickest thickness is 24 mm; the wall thickness has great differences.
3. Because wall thickness of inserts on both sides has great differences, this not only brings difficulties to filling processes of aluminum alloy liquid, but also tests die casts' feeding capacities.
4. Aluminum alloy die casts can easily have blowholes, shrinkage, cracks, shrinkage porosity and other defects; thus, it is difficult to control their quality.
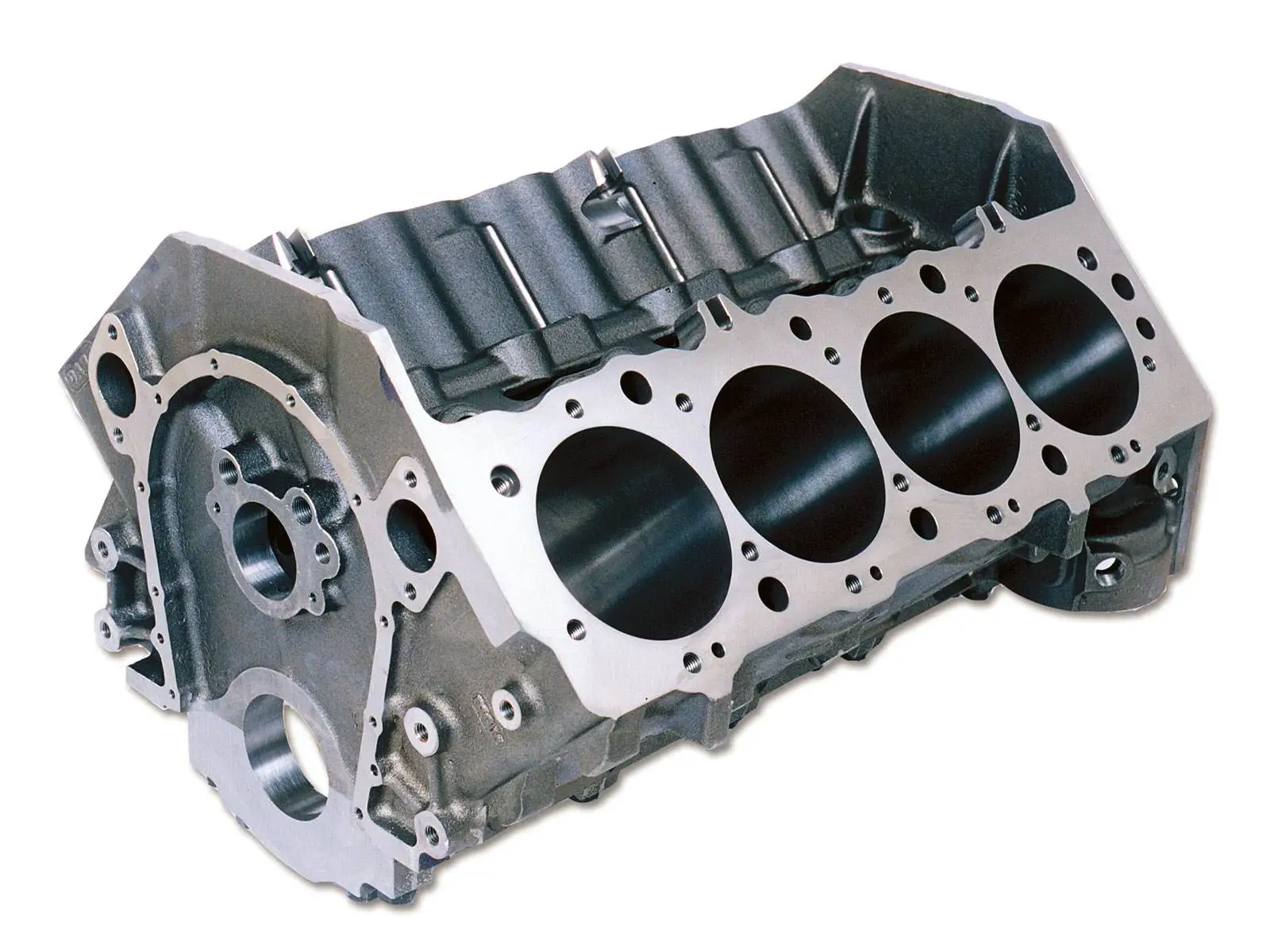