Die casting aluminum refers to the parts formed by the inner cavity's pressure on the molten metal, while
lathe aluminum refers to the parts formed by the direct process of the raw materials by the lathe.
The heat dispersion and good appearance performance of aluminum alloy have made aluminum alloy surpass the current plastic, and aluminum alloy's weight has made it irreplaceable.
1. Material differences:
Die casting aluminum alloy generally adopts ADC12 or ALsi9cu3 materials, while lathe aluminum uses 6063 or 6061 materials.
2. Appearance differences: Die casting aluminum process is equivalent to plastic injection molding process, therefore it can create any shapes. The housing of the street lamp is made from die casting aluminum. The shapes of lathe aluminum uniform sections change slightly, for example, LED bulb heat sinks and aluminum profiles of doors and windows.
3. Thermal conductivity: Generally, the thermal conductivity of
die casting aluminum is about 80-90W/M.K, while the thermal conductivity of
lathe aluminum is about 180-190W/M.K.
4. Costs: Costs of die casting and lathe aluminum are relative, which are calculated by weight and machining. Their costs are calculated according to actual material prices and labors. Relatively speaking, the cost of
die casting aluminum is higher than that of
lathe aluminum, but circumstances alter cases.
5. Production efficiency: The production efficiency of injection molding is certainly higher. It can produce about 1000 molds with batch manufacturing method per day.
Die casting aluminum has stable dimension, and its shrinkage rate is 0.5%.
Lathe aluminum involves more in machining process. Just as its name implies, it has lower efficiency.
6. Applications:
Die casting aluminum generally is widely used for automotive, street light and the current mobile phone industries, while
lathe aluminum is mainly applied to down light,
ceiling light and door & window, etc.
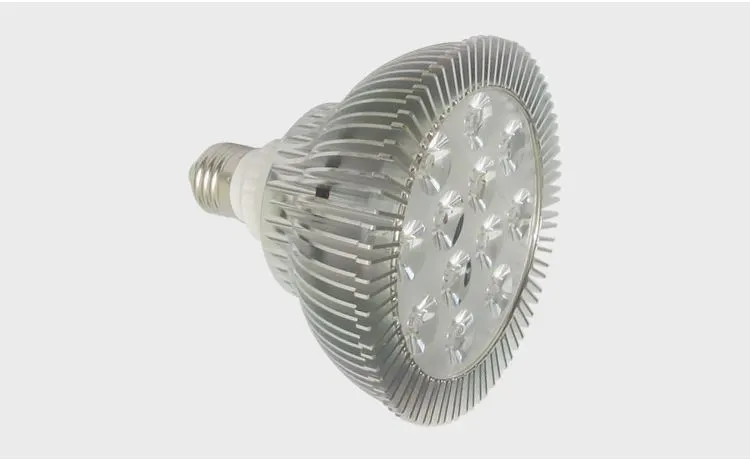